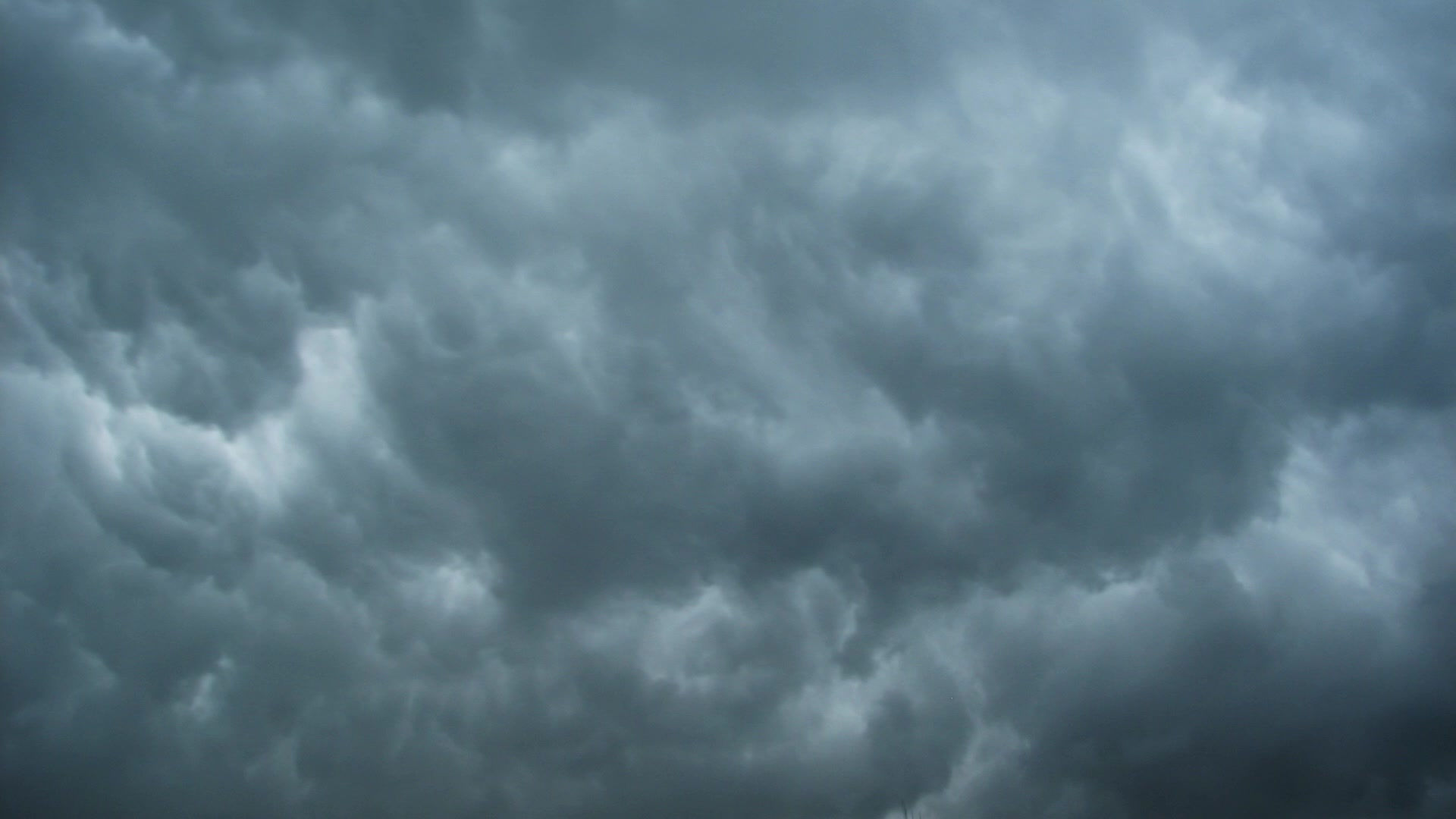
Tube Inspection Projects
Mainly inspection of heat exchangers and air finned coolers tubes using either Olympus MS5800 or Eddyfi Ectane2 inspection system with reporting via Tube Pro 4.0 software (with capability of both 2D and 3D reporting).
​
Internal Rotary Inspection System (IRIS) – an advanced ‘immersed’ ultrasonic testing (UT) performed on heat exchanger tubing of all types of materials (ferrous & non ferrous). It is also commonly used as an inspection for air finned coolers. IRIS is commonly practiced as backup to RFT inspection to double confirm the defects detected by RFT on ferrous tubing.
​
Eddy Current Testing (ECT) – a tube inspection technique via eddy current (electromagnetic) field to detect defects. ECT commonly used for non-ferrous tubing of heat exchangers.
​
Remote Field Testing (RFT) - a tube inspection technique via low frequency eddy current to detect defects on ferrous tubing

TUBE INSPECTION PROJECT LIST
​​
-
SHELL Port Dickson, Malaysia 2011 (Tube Inspection- IRIS) May 2011
Assisting in tube Inspection (IRIS) for heat exchanger in SHELL Port Dickson, Malaysia. Detection on defects via IRIS inspection to detect any possible defects. Inspection, analysis and reporting done by analyst and given to client for further action.
-
PETRONAS MLNG Turnaround 2014 (Tube Inspection- ECT & RFT) May 2014
Tube Inspection (ECT & RFT) for heat exchangers in Petronas MLNG plant in Sarawak, Malaysia. Total project duration (inspection window) of 3 weeks. Detection on defects via Eddy Current Testing for non-ferritic materials and Remote Field Testing for ferritic materials. Inspection done and data acquisition passed to analyst for reporting.
​
-
SPRC, Thailand Turnaround 2014 (Tube Inspection- IRIS, ECT & RFT) June 2014
Tube Inspection (IRIS, ECT & RFT) for heat exchangers and fin fan coolers in Star Petroleum Refining Company (SPRC) plant in Rayong, Thailand. Detection on defects via Eddy Current Testing for non-ferritic materials and Remote Field Testing with backup IRIS inspection for ferritic materials. Main objective of IRIS backup for RFT is to confirm defects due to RFT’s limitation is to screen the tubes and as required by client's inspection scope. IRIS inspection also performed on finned tubes of air finned coolers. Inspection, analysis and reporting done and given to client for further action.
​
-
PTT GSP, Thailand Turnaround 2014 (Tube Inspection- IRIS) July 2014
Tube Inspection (IRIS) for heat exchangers in PTT Gas Separation Plant (GSP) in Rayong, Thailand. Detection on defects on baffle wear that was caused by vibration during operation. Each defect was to be determine in location by length from tube sheet of the exchanger. Inspection, analysis and reporting done and given to client for further action and for record keeping. The client was given 3D reporting for each exchanger for baffle wear tracking and to determine cause of baffle wear.
​
-
PTT PE, Thailand Turnaround 2014 (Tube Inspection- IRIS, ECT & RFT) August 2014
Tube Inspection (IRIS, ECT & RFT) for heat exchangers and fin fan coolers in PTT Polyethelene (PE) plant in Rayong, Thailand. Detection on defects via Eddy Current Testing for non-ferritic materials and Remote Field Testing with backup IRIS inspection for ferritic materials. Main objective of IRIS backup for RFT is to confirm defects due to RFT’s limitation is to screen the tubes and as required by client's inspection scope. IRIS inspection also performed on finned tubes of air finned coolers. Inspection, analysis and reporting done and given to client for further action.
​
-
Tenaga Tube, Malaysia 2014 (Tube Inspection- IRIS) September 2014
Tube Inspection (IRIS) performed for heat exchangers in Tenaga Tube, Nilai, Malaysia fabrication yard. Detection on defects via IRIS inspection to detect any possible defects after fabrication (re-tubing of heat exchangers tube for Petronas) and also for baseline reading of tubes. No defects detected during inspection. Inspection, analysis and reporting done and given to client for further action.
​
-
PTT GC4, Thailand Turnaround 2014 (Tube Inspection- IRIS, ECT & RFT) October - November 2014
Tube Inspection (IRIS, ECT & RFT) for heat exchangers and fin fan coolers in PTT Global Chemical (GC) 4 plant in Rayong, Thailand. Detection on defects via Eddy Current Testing for non-ferritic materials and Remote Field Testing with backup IRIS inspection for ferritic materials. Main objective of IRIS backup for RFT is to confirm defects due to RFT’s limitation is to screen the tubes and as required by client's inspection scope. IRIS inspection also performed on finned tubes of air finned coolers. Inspection, analysis and reporting done and given to client for further action.
​
-
SPRC, Thailand Turnaround 2014 (Tube Inspection- IRIS) November 2014
Tube Inspection (IRIS) for fin fan cooler in Star Petroleum Refining Company (SPRC) plant in Rayong, Thailand. Detection on defects via IRIS inspection to detect corrosion inside the air finned cooler tubes. Inspection, analysis and reporting done and given to client for further action.
​
-
CPOC, Malaysia 2014 (Tube Inspection- IRIS) December 2014
Tube Inspection (IRIS) performed for heat exchangers in CPOC, Rawang, Malaysia fabrication yard. Detection on defects via IRIS inspection to double confirm previous Eddy Current Testing on the tubing. Previous inspection done on the stainless-steel heat exchangers were noted with wall loss in middle section of tubes. Prior to IRIS inspection, defects were noted which believed to be a joint butt weld of tubing. However, joint tubes are not allowed in heat exchangers tubing and fabricator shall be responsible to re-tube the exchangers. Inspection, analysis and reporting done and given to client for further action.
​
-
PTT GSP, Thailand Turnaround 2014 (Tube Inspection- IRIS) December 2014
Tube Inspection (IRIS) for heat exchangers in PTT Gas Separation Plant (GSP) in Rayong, Thailand. Detection on defects on baffle wear that was caused by vibration during operation. Each defect was to be determine in location by length from tube sheet of the exchanger. However, during inspection, severe corrosion throughout the tubes were noted on one of the exchangers. The client extended scope for 100% inspection which took the team in total of 2 weeks to complete. Inspection, analysis and reporting done and given to client for further action and for record keeping. The client was given 3D reporting for each exchanger for baffle wear tracking and to determine cause of baffle wear.
​
-
SPRC, Thailand Turnaround 2015 (Tube Inspection- IRIS & RFT) March 2015
Tube Inspection (IRIS & RFT) for heat exchangers in Star Petroleum Refining Company (SPRC) plant in Rayong, Thailand. Detection on defects via Remote Field Testing with backup IRIS inspection for ferritic materials. Main objective of IRIS backup for RFT is to confirm defects due to RFT’s limitation is to screen the tubes and as required by client's inspection scope. Inspection, analysis and reporting done and given to client for further action
​
-
Shell F23 Platform, Malaysia Offshore 2015 (Tube Inspection- IRIS) April 2015
Tube Inspection (IRIS) for fin fan coolers in Shell F23 Platform, Malaysia 2015. Total shutdown period was 21 days as for preparations of permit, cleaning of fin fan cooler tubes by the cleaning team, pre-inspection and IRIS inspection on tubes. Inspection, analysis and reporting done and given to client for further action.
​
-
Shell Lutong Boiler Tubes 2016 (Tube Inspection- IRIS) May 2015 – June 2015
Tube Inspection (IRIS) on boiler tubes in Shell Lutong, Malaysia 2015. Client requested to inspect 4 unit of boilers in their facility with multiple trips (boilers couldn't be offline simultaneously for cleaning and inspection). Boiler tubes were successfully inspected even though the tubes facing difficulties to be flooded with water (water acts as couplant for IRIS as medium for ultrasonic signals transmission). Inspection, analysis and report given to client for further action.
​
-
PTT I4, Thailand Turnaround 2015 (Tube Inspection- IRIS, ECT & RFT) July 2015
Tube Inspection (IRIS, ECT & RFT) for heat exchangers and fin fan coolers in PTT Global Chemical I4 plant in Rayong, Thailand. Detection on defects via Eddy Current Testing for non-ferritic materials and Remote Field Testing with backup IRIS inspection for ferritic materials. Main objective of IRIS backup for RFT is to confirm defects due to RFT’s limitation is to screen the tubes and as required by client's inspection scope. IRIS inspection also performed on finned tubes of air finned coolers. Inspection, analysis and reporting done and given to client for further action.
​
-
PTT Glycol, Thailand Turnaround 2015 (Tube Inspection- IRIS, ECT & RFT) July 2015
Tube Inspection (IRIS, ECT & RFT) for heat exchangers and fin fan coolers in PTT Glycol plant in Rayong, Thailand. Detection on defects via Eddy Current Testing for non-ferritic materials and Remote Field Testing with backup IRIS inspection for ferritic materials. Main objective of IRIS backup for RFT is to confirm defects due to RFT’s limitation is to screen the tubes and as required by client's inspection scope. IRIS inspection also performed on finned tubes of air finned coolers. Inspection, analysis and reporting done and given to client for further action.
​
-
PTT GC5, Thailand Turnaround 2015 (Tube Inspection- IRIS, ECT & RFT) August 2015
Tube Inspection (IRIS, ECT & RFT) for heat exchangers and fin fan coolers in PTT Global Chemical (GC) 5 plant in Rayong, Thailand. Detection on defects via Eddy Current Testing for non-ferritic materials and Remote Field Testing with backup IRIS inspection for ferritic materials. Main objective of IRIS backup for RFT is to confirm defects due to RFT’s limitation is to screen the tubes and as required by client's inspection scope. IRIS inspection also performed on finned tubes of air finned coolers. Inspection, analysis and reporting done and given to client for further action.
​
-
PTT GSP, Thailand Turnaround 2015 (Tube Inspection- IRIS) September 2015
Tube Inspection (IRIS) for heat exchangers in PTT Gas Separation Plant (GSP) in Rayong, Thailand. Detection on defects on baffle wear that was caused by vibration during operation. Each defect was to be determine in location by length from tube sheet of the exchanger. Inspection, analysis and reporting done and given to client for further action and for record keeping. The client was given 3D reporting for each exchanger for baffle wear tracking and to determine cause of baffle wear.
​
-
Petronas Penapisan Melaka (PPM), Malaysia Shutdown 2015 (Tube Inspection- ECT & RFT) November 2015
Being part of the tube inspection team for Petronas Penapisan Melaka shutdown 2015. Performing Eddy Current Testing (ECT) for non-ferritic materials and Remote Field Testing (RFT) for ferritic materials inspection for heat exchangers. Inspection, analysis & reporting done and given to the turnaround coordinator for further submission to the client.
​
-
TNB Janamanjung, Malaysia (Tube Inspection- ECT & RFT) November 2015
ECT & RFT inspection were performed on heat exchangers tubes for TNB Janamanjung shutdown 2015. Inspection and reporting done and given to client.
​
-
SCG, Thailand Turnaround 2015 (Tube Inspection- IRIS & RFT) December 2015
Tube Inspection (IRIS & RFT) for heat exchangers in SCG plant in Rayong, Thailand. Detection on defects via Eddy Current Testing for non-ferritic materials and Remote Field Testing with backup IRIS inspection for ferritic materials. Main objective of IRIS backup for RFT is to confirm defects due to RFT’s limitation is to screen the tubes and as required by client's inspection scope. Inspection, analysis and reporting done and given to client for further action.
​
-
Woodside Australia in Singapore Sembawang Shipyard (Tube Inspection- ECT & RFT) February 2016
Tube Inspection (ECT & RFT) for heat exchangers for Woodsite in Singapore Sembawang Shipyard 2016. Inspection done for OKHA Fremantle FPSO. Detection on defects via Eddy Current Testing for non-ferritic materials and Remote Field Testing for ferritic materials. Inspection, analysis and reporting done and given to client for further action. Discussion with client on NDT site & technical issues.
​
-
PTT GC11, Thailand Turnaround 2016 (Tube Inspection- IRIS, ECT & RFT) March 2016
Tube Inspection (IRIS, ECT & RFT) for heat exchangers and fin fan coolers in PTT Global Chemical (GC) 11 plant in Rayong, Thailand. Detection on defects via Eddy Current Testing for non-ferritic materials and Remote Field Testing with backup IRIS inspection for ferritic materials. Main objective of IRIS backup for RFT is to confirm defects due to RFT’s limitation is to screen the tubes and as required by client's inspection scope. IRIS inspection also performed on finned tubes of air finned coolers. Inspection, analysis and reporting done and given to client for further action.
​
-
PTT GSP, Thailand Turnaround 2016 (Tube Inspection- IRIS) March 2016
Tube Inspection (IRIS) for heat exchangers in PTT Gas Separation Plant (GSP) in Rayong, Thailand. Detection on defects on baffle wear that was caused by vibration during operation. Each defect was to be determine in location by length from tube sheet of the exchanger. Inspection, analysis and reporting done and given to client for further action and for record keeping. The client was given 3D reporting for each exchanger for baffle wear tracking and to determine cause of baffle wear.
​
-
RPCM Gebeng, Malaysia Shutdown 2016 (Tube Inspection- ECT & RFT) April 2016
Tube Inspection (ECT & RFT) for heat exchangers for RPCM Gebeng, Malaysia Shutdown 2016. Detection on defects via Eddy Current Testing for non-ferritic materials and Remote Field Testing for ferritic materials. Inspection, analysis and reporting done and given to client for further action.
​
-
PTT GSP, Thailand Turnaround 2016 (Tube Inspection- IRIS) May 2016
Tube Inspection (IRIS) for heat exchangers in PTT Gas Separation Plant (GSP) in Rayong, Thailand. Detection on defects on baffle wear that was caused by vibration during operation. Each defect was to be determine in location by length from tube sheet of the exchanger. Inspection, analysis and reporting done and given to client for further action and for record keeping. The client was given 3D reporting for each exchanger for baffle wear tracking and to determine cause of baffle wear.
​
-
PTT GC6, Thailand Turnaround 2016 (Tube Inspection- IRIS, ECT & RFT) May - June 2016
Tube Inspection (IRIS, ECT & RFT) for heat exchangers and fin fan coolers in PTT Global Chemical (GC) 6 plant in Rayong, Thailand. Detection on defects via Eddy Current Testing for non-ferritic materials and Remote Field Testing with backup IRIS inspection for ferritic materials. Main objective of IRIS backup for RFT is to confirm defects due to RFT’s limitation is to screen the tubes and as required by client's inspection scope. IRIS inspection also performed on finned tubes of air finned coolers. Inspection, analysis and reporting done and given to client for further action.
​
-
Petrofac Chendor FSO Shutdown 2016 (Tube Inspection- RFT) August 2016
Tube Inspection for heat exchanger in Petrofac Chendor FSO, Malaysia Shutdown 2016. Detection on defects via Remote Field Testing for ferritic material (carbon steel) of the heat exchanger tubes. Common practice is to back up with IRIS inspection to double confirmation of defects by RFT inspection (as RFT is more to screening of tubes and as required by client's inspection scope) but in this shutdown, IRIS was not performed due to restriction of water to flood the tubes. Due to presence of ‘turbulator’ strips (twisted strips inside each tube to increase the turbulence flow of the exchanger) of the heat exchanger tubes, the original scope was reduced to avoid such delay in inspection time. Inspection, analysis and reporting done and given to client for further action.
​
-
Shell Labuan Crude Oil Terminal (LCOT), Malaysia 2016 (Tube Inspection- IRIS) October 2016
Tube Inspection (IRIS) for heat exchangers in Labuan Crude Oil Terminal (LCOT), Malaysia shutdown 2016. IRIS inspection is performed on ferritic materials (e.g. carbon steel) to detect wall loss in tubes. Inspection, analysis and reporting done and given to client for further action.
​
-
Phu My Fertilizer, Vietnam 2016 (Tube Inspection- IRIS) November 2016
Tube Inspection were to be performed at Phu My Fertilizer plant, Vietnam 2016. The main inspection scope was IRIS inspection on heat exchanger and given only a 6 hours inspection window due to short period of production shutdown time. The client only require IRIS operator and inspection equipment was supplied by client. Due to inspection equipment failure (UT motherboard suspected to be damaged and was not check by client before), the inspection was cancelled. Client decided to only depend on pressure test result and will do inspection during shutdown 2017.
​
-
Petron Bataan, Phillipines 2016 (Tube Inspection- IRIS) December 2016
Tube Inspection (IRIS) was performed on fin fan coolers to inspect and monitor wall loss in tube thickness. The main objective of the inspection was to inspect, determine the remaining thickness and to monitor the corrosion rate of the fin fan coolers due to some corrosion detected in the previous inspection. The corrosion occurs due to the turbulence and temperature change at the inlet section of the air finned coolers. Initially, the client applied anti-corrosion sleeves yet the sleeves length was not sufficient enough to protect the tubes (wall loss was detected approximately 100mm after tube lips). Inspection, analysis and reports given to client for further action.
​
-
Petronas Tiong-A Platform, Malaysia (Tube Inspection- IRIS) February 2017
Tube Inspection for fin fan coolers in Petronas Tiong-A platform. Detection on defects via IRIS inspection done on finned tubes of the air fin cooler. The inspected fin fan cooler had to be inspected 100% due to severe wall loss detected previously in the original scope of inspection. Inspection, analysis and reporting done and given to client for further action.
​
-
PTT Phenol, Thailand Turnaround 2017 (Tube Inspection- IRIS, ECT & RFT) March 2017
Tube Inspection (IRIS, ECT & RFT) for heat exchangers and fin fan coolers in PTT Phenol plant in Rayong, Thailand. Detection on defects via Eddy Current Testing for non-ferritic materials and Remote Field Testing with backup IRIS inspection for ferritic materials. Main objective of IRIS backup for RFT is to confirm defects due to RFT’s limitation is to screen the tubes and as required by client's inspection scope. IRIS inspection also performed on finned tubes of air finned coolers. Inspection, analysis and reporting done and given to client for further action.


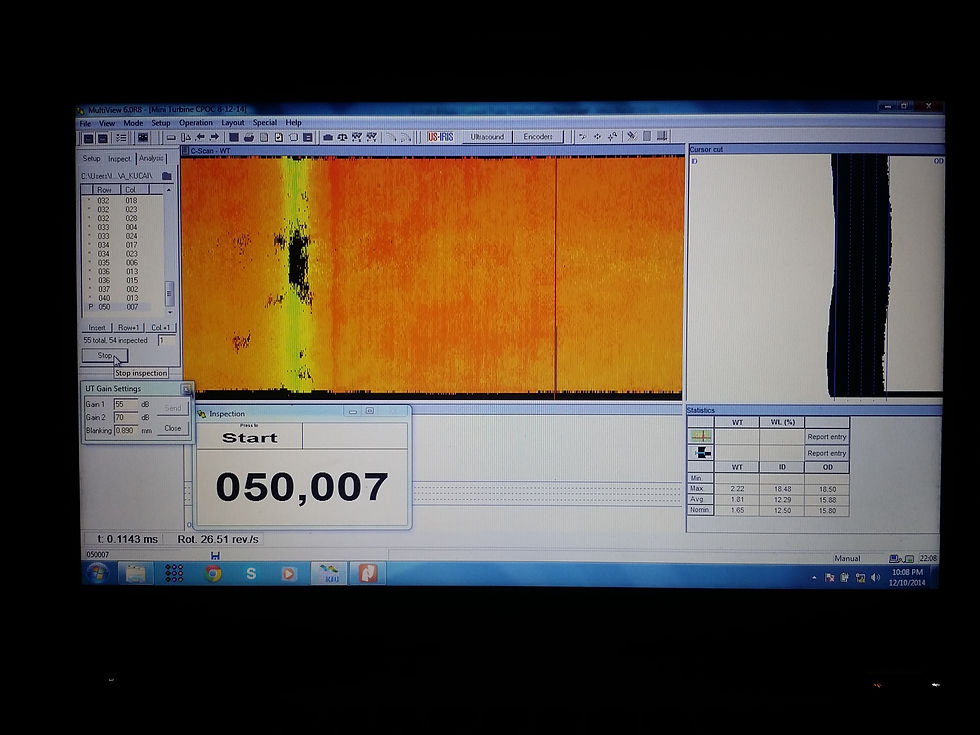
